Schedule coordination & collaboration: Partners working towards a common first patient date
The University of Kansas Health System Proton Therapy Project
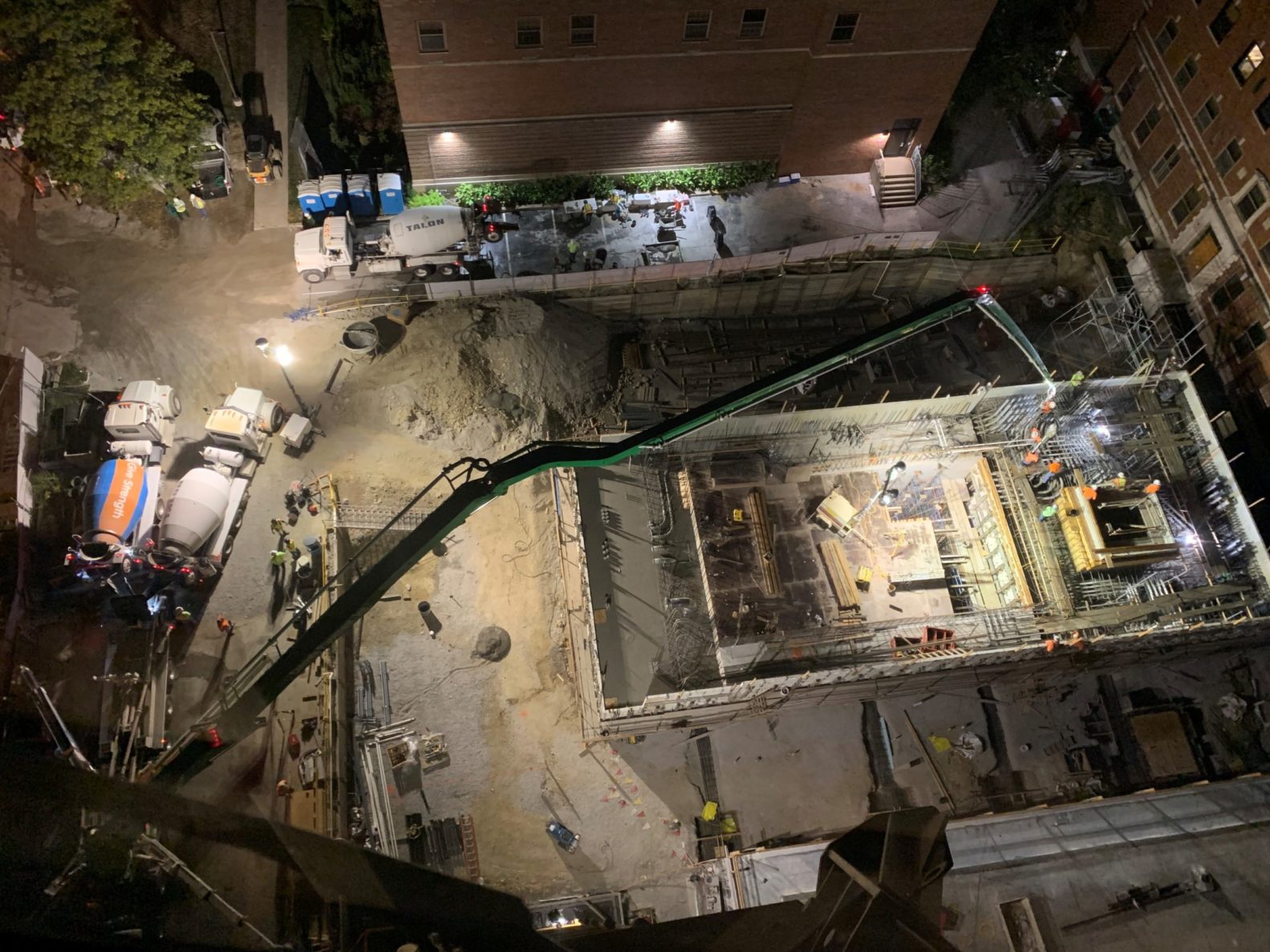
The University of Kansas Health System (TUKHS) is bringing proton therapy, the most technologically advanced form of radiation treatment, to Kansas City to provide treatment for the two states and surrounding region. This is the first proton therapy facility in Kansas. TUKHS set a goal to see the first patient in 2022. With that date in mind, the JV team of McCownGordon and Linbeck worked backwards to accomplish this goal. The team knew the proton therapy equipment takes 14 months from procurement to arrival and 12 months to calibrate. Knowing these key time frames, the team used pull planning coordination sessions on weekly basis throughout the life of the project to coordinate designers, vendors and trade partners working in different cities, states, countries and continents
They created a project schedule (design and construction) and, on a parallel path, the equipment schedule (selection, fabrication, shipping/rigging, installation and commissioning). By working backwards, the team created a detailed schedule and got buy-in and approval from all involved.
Project Schedule
This project sits on a half-acre off a busy street taking up 90% of the site. Because of the tight site, the team knew they needed to collaborate with trade partners early and often. They walked all trades through the pull planning schedule, indicating the deadlines and worked with them for on-time deliveries. Once a truck pulled in with supplies, the team had to unload and put those items to use.
One of the major trades the team worked with for precise coordination was our concrete trade partners. They helped with the mass concrete pours for the vault. With 10 pours equaling 280 trucks (2,721 yards/ 10,998,010 lbs. of concrete), the team had to time the pours to precision. With one chance to be successful per pour, back up pump trucks and concrete plants were on call and on the ready if something were to not go as planned. Heavy coordination with the surrounding buildings, campus PD, weather forecasts/ temperatures, and traffic patterns were taken into consideration for every pour. To help maintain concrete curing temperatures, decrease traffic on the major roadway, most pours started just after midnight and lasted through to noon the next day.
Although placement of the concrete was key, the management of the thermal control plan post placement was crucial to be successful. Maintaining constant temperatures throughout the sections of the pours was completed using hourly temperature loggers within the pours and taking preplanned actions to manage the thermal properties until they reached their peak and began to reduce. Typically, this process lasted three to four days, with constant review and action to provide the necessary qualities to ensure shielding of the radiation particles remained contained within the vault.
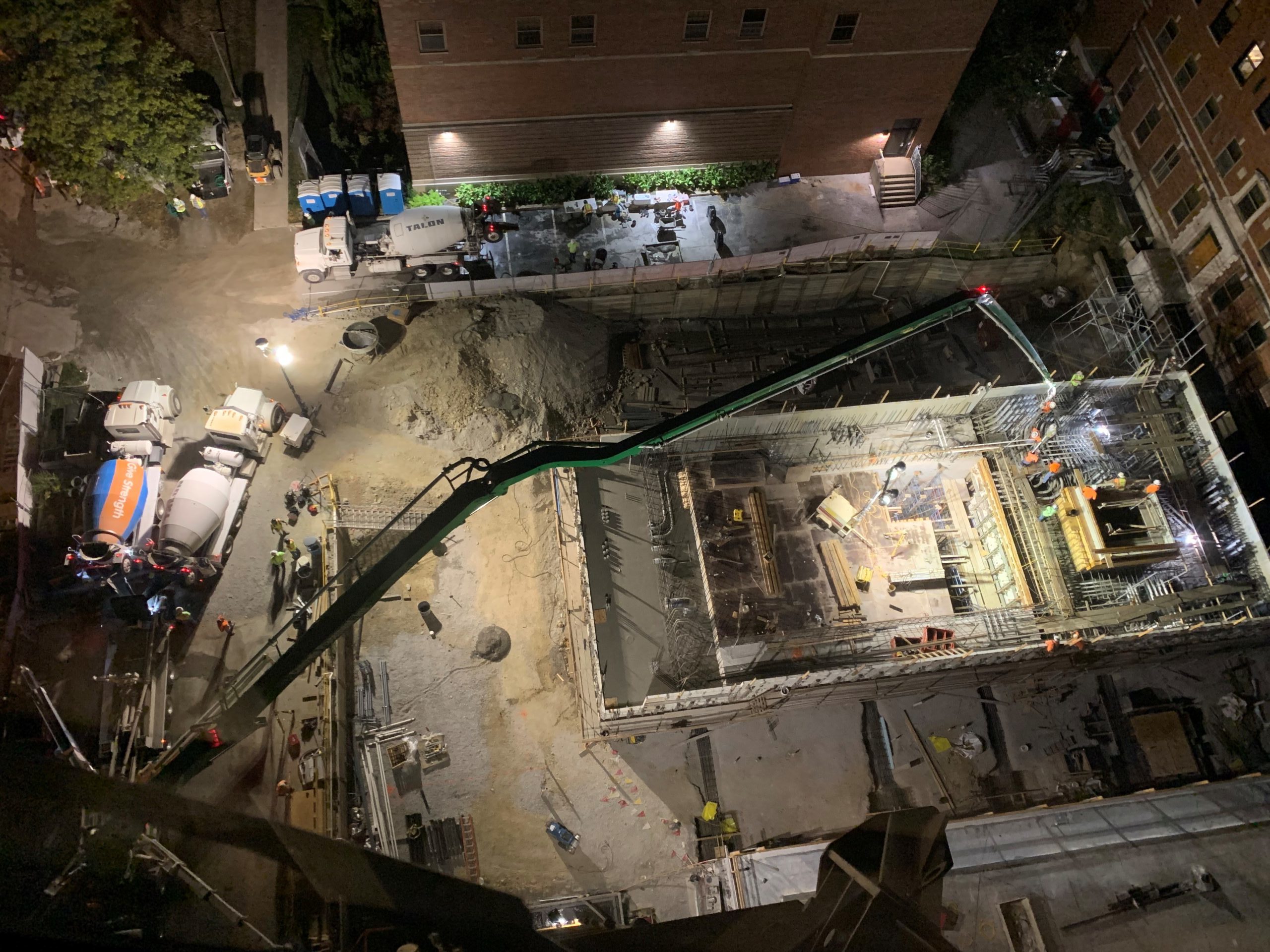
Equipment schedule
The equipment selection process was already complete before McCownGordon + Linbeck came on board. Once selected, the fabrication of the proton therapy equipment takes 14 months. The gantry and cyclotron, manufactured by IBA, (weighing roughly 130 tons together) then traveled across the ocean from Belgium, into the Port of Houston and north to The University of Kansas Health System in Kansas City, KS. The team coordinated with IBA from the beginning to ensure the project schedule aligned with the equipment delivery schedule.
While it was in route, the University of Kansas Health System tracked it for all to watch. In an article they noted “The equipment will travel in a convoy of six semi-tractor trailers, leaving Houston later in March, for its 10-day journey to Kansas City. The equipment is so massive that it requires a police escort in each state it travels through. Our technology vendor, IBA, works with each state’s Department of Transportation to determine the route through the state and the number of police escorts required. Because of the equipment’s considerable size, a refueling truck travels with the convoy to replenish fuel. The trucks transporting the equipment are too large to refuel at gas stations. The convoy includes two bucket trucks and power line operators who must move/replace power lines to allow passage of the immense equipment.”
Watch the video of the gantry and cyclotron making it’s way to Kansas City
With the small half-acre site and limited turning radiuses, transportation/ rigging and site logistics planning was of the utmost importance to ensure a successful install. Maneuvering 160’ and 120’ long equipment trailers within the tight site was completed as planned to locate the gantry and cyclotron for hoisting. Once the equipment was on site, hoisting the gantry off the truck was completed with two cranes, rotated, and then rigged into its final location within the vault with a 500-ton crane. Hoisting the 70-ton gantry into its final position required 10 hours to perfectly align within the concrete vault.
Watch video of gantry being positioned
Once all the equipment was placed and aligned, the final infill of the vault roof was completed with double stacked precast beams and planks. Over the next 10 months the equipment vendor completes install, begins to generate the beam and works through calibrating all parts and pieces.